See This Report about Indonesia Furniture Manufacturers
Indonesia Furniture Manufacturers Fundamentals Explained
Table of ContentsExamine This Report about Indonesia Furniture ManufacturersHow Indonesia Furniture Manufacturers can Save You Time, Stress, and Money.8 Easy Facts About Indonesia Furniture Manufacturers ShownIndicators on Indonesia Furniture Manufacturers You Need To KnowIndicators on Indonesia Furniture Manufacturers You Need To Know
There are some drawbacks to buying from a furnishings supplier. For one, you might have to wait longer to get your furnishings since it's being tailored. In addition, you may not have the ability to see or touch the product before you acquire it. A furniture retailer is a firm that offers furnishings made by various suppliers.When you purchase from a furniture retailer, you're buying an item of furnishings that's currently been made and is prepared to be shipped to your home. One of the benefits of purchasing from a furnishings retailer is that you can typically see and touch the item prior to you purchase it.
At BH Furnishings, our team believe in establishing brand-new standards for excellence in the manufacturing of commercial furnishings - Indonesia furniture manufacturers. Our dedication to advancement has actually led us to accept cutting-edge automation innovation, transforming the means we produce furnishings and driving us to the center of the industry. Gone are the days of manual work dominating the production flooring
Our machinery functions effortlessly, assisted by the accurate parameters established by our proficient designers, ensuring consistently high-quality outcome. Claim farewell to production hold-ups and overtime expenses. Our automated systems run tirelessly, 24/7, assuring a stable and uninterrupted process. This suggests we not only satisfy but surpass delivery target dates, offering our customers with a level of integrity that typical manufacturing techniques merely can not match.
The 5-Minute Rule for Indonesia Furniture Manufacturers
Our manufacturing capability has soared, enabling us to satisfy the demands of even the biggest projects without endangering on quality. As your companion in industrial furnishings remedies, we can easily scale our result to accommodate your requirements, despite the range. While standard production depends heavily on manual work, our automated systems have dramatically reduced our dependancy on a big labor force.
Furniture production is a complicated process that entails various phases, from developing and product selection to production and setting up. At each phase, there is a possibility of problems or errors that can compromise the quality of the final product. To guarantee that furnishings is of premium quality, furniture suppliers carry out quality assurance processes to recognize and correct any type of concerns that may occur during manufacturing.
The examination process should cover numerous facets, such as setting up, coating, colour, style, packaging, labelling, and marking. By implementing a rigorous evaluation procedure, manufacturers can ensure their items satisfy the essential quality, safety, and longevity needs. They additionally give the flexibility to attend to concerns and make adjustments prior to finishing the final product.
Furnishings quality standards are sets of guidelines and demands for furnishings production. They specify the required top quality level of furnishings manufacturing and cover aspects such as safety, resilience, strength, and ecological effect.
Not known Incorrect Statements About Indonesia Furniture Manufacturers

To guarantee their furniture products can withstand different climate components, consisting of sunlight, rain, snow, and wind, manufacturers should think about worldwide acknowledged criteria that comprise examinations and screening. Here are some of the standards to maintain in mind: ASTM F1561-03 is a global typical developed by the American Section of the International Association for Screening Materials (ASTM).
UL 962 is a worldwide security requirement developed by Underwriters Laboratories (UL), an independent worldwide supply safety solutions firm. The standard applies to house and industrial home furnishings, consisting of exterior furnishings.
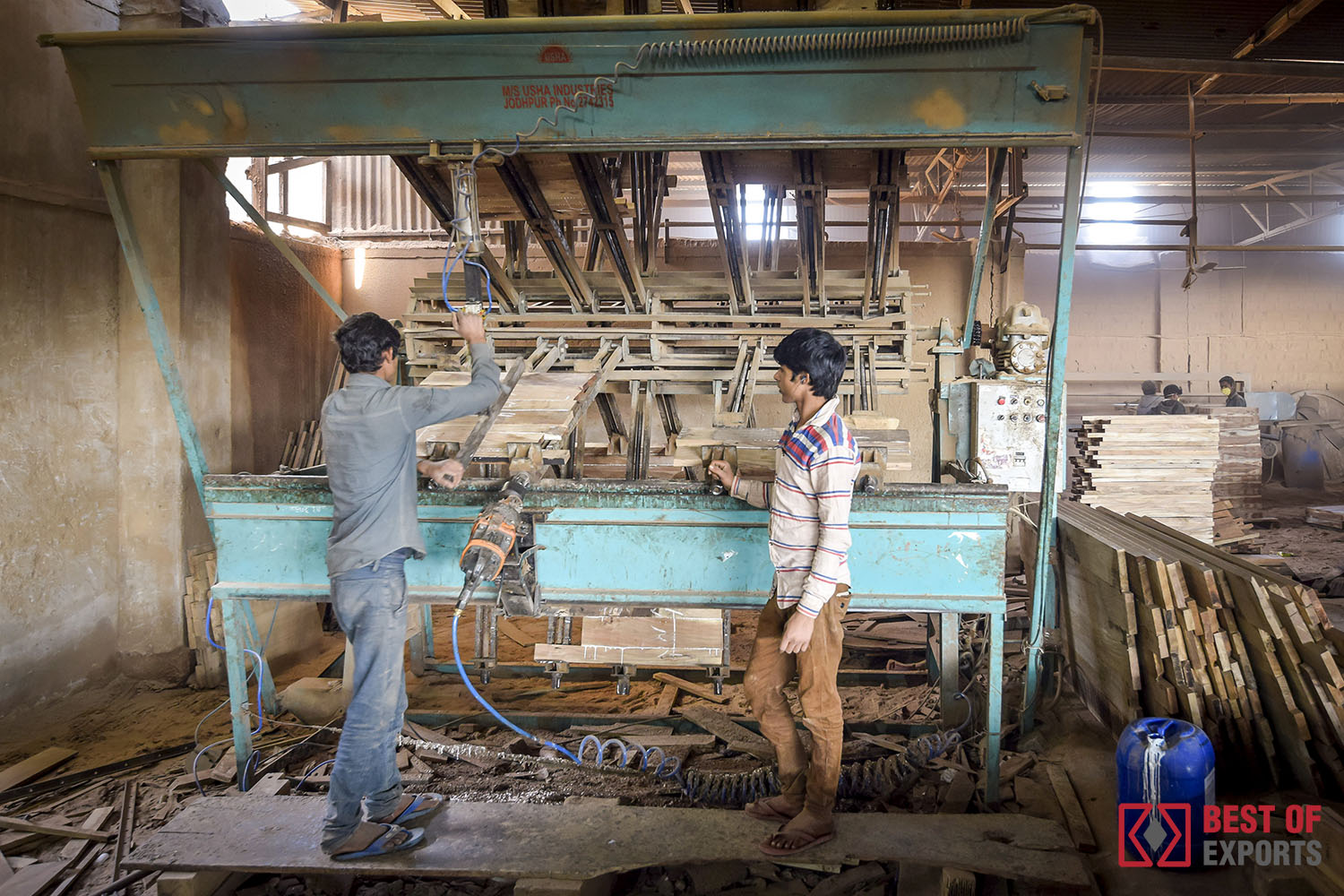
Indonesia Furniture Manufacturers Things To Know Before You Get This
It aids to identify problems in the furnishings and review its performance and conformity with the called for quality standards. These samples normally represent the different types of furnishings that they create.
This might involve a combination of various tests, consisting of strength testing, sturdiness screening, safety and security testing, and environmental effect testing. The examples are then tested for various quality criteria, such as stamina, toughness, safety and security, and ecological impact. The outcomes are after that assessed to establish whether the items meet the required top quality standards.

Normally, every retail store furniture is different. All projects have regarding a month's time in between layout ideation and final production. This is where the major challenge lies. Layouts conference customer convenience Taking full advantage of room usage in storage, display screen, footfall, visitor seats and walkways read this Making certain simplicity of accessibility to items for tests and purchase Designing modular furniture that is very easy to relocate and recondition Fulfilling safety and security demands of consumers A fast TAT from layout to manufacturing and setup with very little errors can help address the above concerns.
Top Guidelines Of Indonesia Furniture Manufacturers
Also, a developer can understand the market trends and prepare with cutting-edge layouts in advance. Read below: How DriveWorks Aids You to Reduce Lead Time in Production Developers usually need to transform the shapes and sizes of furnishings at a moment's notice. These might have different visual and useful needs like front workdesk, and servicing workdesk that vary in measurements.
Boosts item high quality and lowers scrap. Area guideline documents along with amount departures are also created for retail shop furnishings installations. Style versions and problems are decreased, and the store floor can begin producing on the day of sales.
It is Go Here an extremely competitive market, with companies making every effort to maintain up with altering customer needs and the newest technological trends. Today's customers are much more likely to favor furniture that is personalized and made with sustainable materials.